Here’s What We Can Learn From Japanese Prefab Homes
Thanks to cutting-edge design, mass production, and customization, prefabricated housing is common practice in Japan.
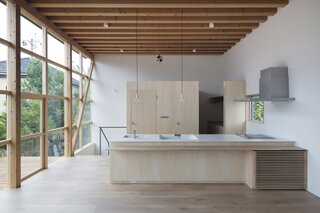
Thanks to cutting-edge design, mass production, and customization, prefabricated housing is common practice in Japan.
The highly innovative Japanese prefab housing industry has developed a user-orientated approach by integrating specially developed marketing, design and quality-orientated techniques into its production processes. Customization is delivered through holistic management and balancing the use of standard components with flexibility of assembly. With manufacturers continually striving to bridge the communication gap between themselves and their clients to offer successful mass-customized designs, homebuyers benefit from a sense of ownership and individuality. In turn, the manufacturers benefit from customer satisfaction and a positive reputation in the market.
Prefab Housing in Japan
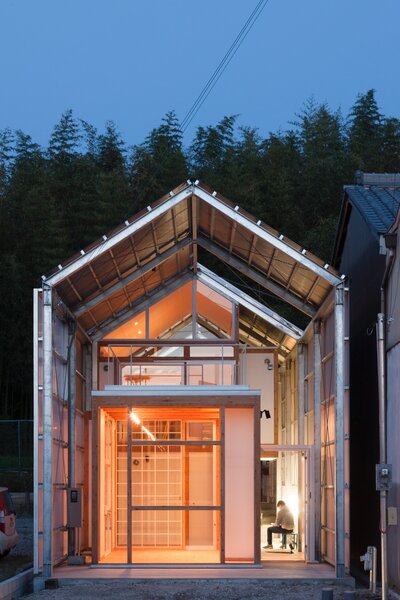
Next to the Todaiji Temple in Nara, Japan, House of 33 Years by architectural firm Assistant takes its name from the clients, an elderly couple who hadn’t moved from their previous home for 33 years.
© Shinkenchiku Sha
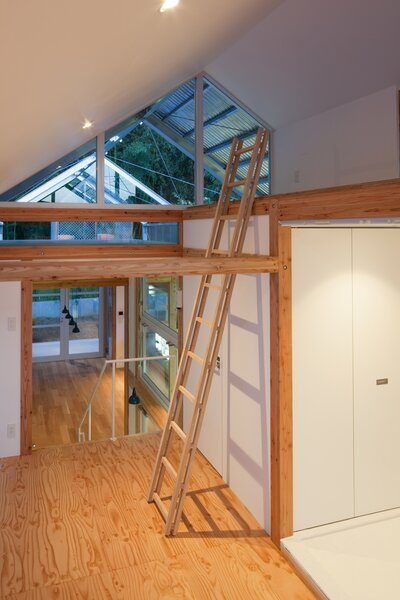
Built in three different cities and supported by the Aomori Contemporary Art Centre and Sendai School of Design, House of 33 Years comprises an exterior steel roof that was built on site and a series of pavilions and timber rooms underneath it.
© Shinkenchiku Sha
Japan’s prefabricated-housing industry is a world leader in innovation, with efficient production processes, targeted marketing strategies and consumer outreach, and high-quality designs that offer variability and flexibility at affordable prices. A fully computerized system enables clients to customize their homes with standardized components. Unlike the common Western perception about prefabrication, in Japan factory-manufactured houses are seen as superior to conventionally built ones.
In the post-war period, Japan began experimenting with prefab housing to meet demand, and factory manufacturing became more popular. One of the reasons behind this trend was that houses have a short lifespan in Japan—an average of twenty-six years—and homebuyers often prefer to build their own. The country’s population is roughly twice that of the UK, yet over six times as much new housing is built in Japan than in the UK each year. A family that outgrows its home will simply tear it down and build a new one on the same site, and some companies now offer deals for house replacement: a maximum fifty-day period (including weekends) from moving out to moving in. This style of construction makes a fully customizable production process particularly advantageous.
The urgent demand for housing in the 1960s and ’70s also provided an opportunity, as conventional home construction was unable to saturate the housing market owing to a shortage of materials and labor. As a result, manufactured homes provided an affordable alternative, drastically accelerating their wider acceptance.
Marketing Strategies and Consumer Outreach
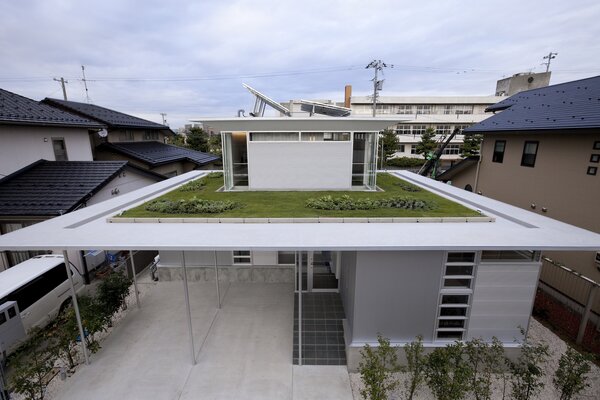
In 2008, Atelier Tekuto received a grant to build an all-aluminum home as part of Japan’s efforts to reduce the construction industry’s carbon footprint. The resulting A-Ring in Ishikawa, Japan, builds on the firm’s previous explorations and is named for its structure: four aluminum molds interlock to form a durable, efficient, low-waste ring.
Toshihiro Sobajima
See the full story on Dwell.com: Here’s What We Can Learn From Japanese Prefab Homes
Related stories: