Season Three Breaks Down the Design Process Behind The Ansel
Season Three founders share how The Ansel hiking boot came to be and how they're made in Northern Italy.
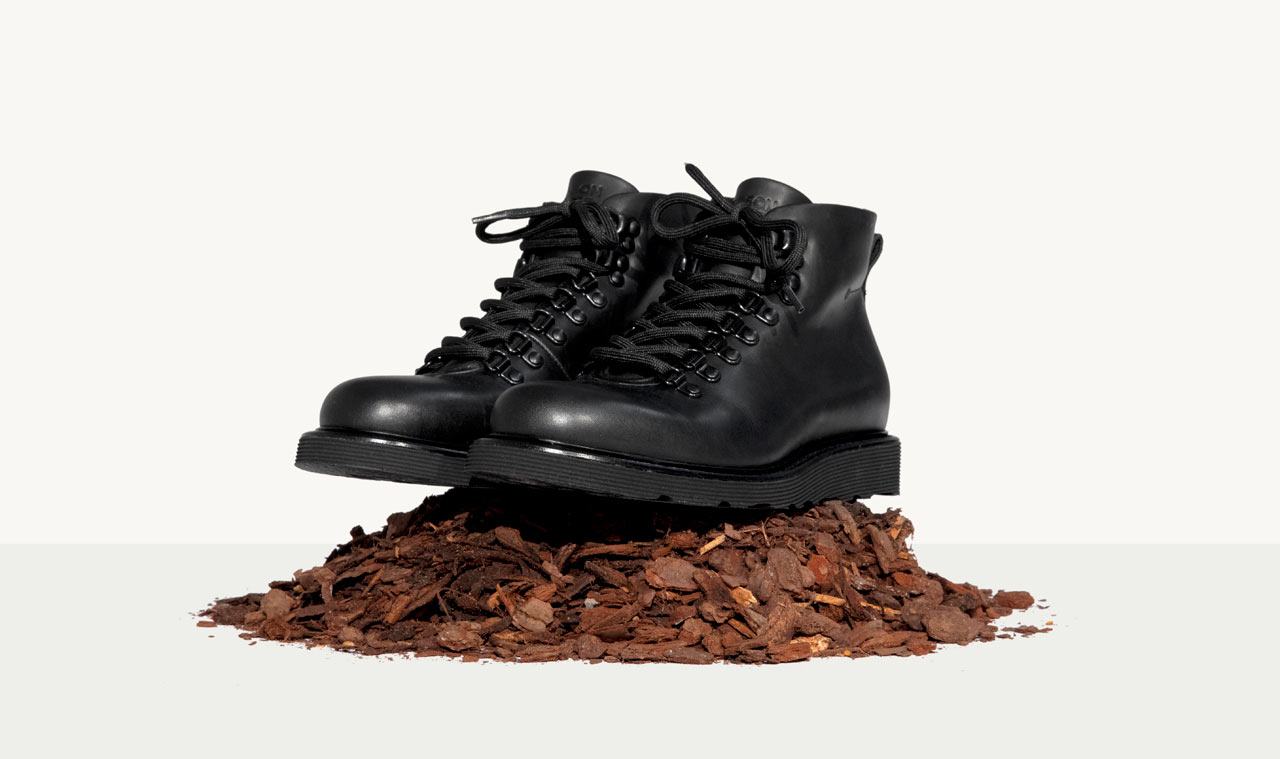
Founded in 2018 by Jared Johnson and Adam Klein, Season Three is a contemporary outdoor apparel brand conceived while the two were (self-described) highly-opinionated graduate students at MIT. Influenced by art and creative culture, the duo recently launched their first product, The Ansel, a genderless, all-weather hiking boot that easily transitions from the trails to work, and even a museum, with its rugged yet fashionable aesthetic. The road to get to the finished product included over 50 prototypes, but by the looks of it, the lengthy design process was worth it. For this month’s Deconstruction, Season Three’s founders share how The Ansel boot came to be and more about the manufacturing process in Northern Italy. Take a look.
Our designer in Italy began with line sketches. We WhatsApp-ed edits back and forth for two months before locking in the technical sketches that the factory would need to produce a prototype. We opted for a more traditional design but added a few novel features – a split seam back (which allows the wearer to put the boot on easier) and a fully gusseted tongue with a “winged” design (which keeps water, dirt, and ice from seeping in).
This is a technical sketch that we provided the factory. Versus the line sketches, this document details the proportions and materials to be used.
We learned that Vibram’s US headquarters is in Boston so we reached out to let them know we were designing a hiking boot with our factory in Italy. They were gracious enough to send us a bunch of sole samples, saving us hundreds of dollars in international shipping costs.
We received our first batch of prototypes about four months into our journey. The first thing that struck us was the quality of the materials. Some of the leathers that we picked out were so exquisite that they had no business being on a boot; we’re talking about Prada handbag-quality leathers, which cost 70 Euros a linear meter.
We became obsessed with leather samples. We visited a number of trade shows to collect swatch samples and build relationships with tanneries from all over the world. Although we were impressed with some of the leathers from outside of Italy, we decided to go with Italian leathers to lower our carbon footprint.
Our design iteration process was intense. We created dozens of markups like this one, encouraging our factory to experiment with different materials, colors, and components. We definitely went overboard, but stopped just short of the relationship ruining line, being merely “annoying”.
The manufacturing process begins with the creation of the last. Once our technical design was locked in, we were able to order a custom molded last that our boot could be built on. We wanted to create a roomy and comfortable inside, but a narrow silhouette on the outside. For cost and complexity reasons, all of our samples were done on a EU size 42 last, which translates to a US men’s size 9/9.5. At production, we needed to develop our custom last for our full size range – 18 different men’s and women’s sizes (including half sizes). One of the main reasons footwear is so difficult is sizing issues. Luckily, we comp out really well to what the consumer’s Nike sneaker size is, minus ½ a size (Ex. size 11 in Nike, is a 10.5 in a Season Three Ansel boot.
This is where the pattern cutting and sewing process takes place for our boot’s upper, amazing craftspeople with decades of experience cut and sew each upper to our unique specifications by hand, fasten the D-rings and hooks, and stitch the leather components together.
This is what the upper pattern for The Ansel looks like before it is applied to the last.
This machine affixes the upper pattern to the last for three to five days to form the shape of the boot. This time is a bottleneck, but ensures the boots shape and longevity is not compromised over time.
This is what The Ansel looks like after the leather has formed to the last.
This is a side view of the upper after being taken off the last. You can also see that beautiful full merino interior.
The upper is then taken off the last and affixed to the fiberboard footbed. We toyed around with the idea of using a wood footbed, which is very old world, but top quality construction, however, we ultimately decided that comfortability was more important in the sole.
The upper leather is sanded to the footbed, getting rid of any excess lumps that would make the sole uncomfortable when the sole is applied through the goodyear welting process.
We always knew that we wanted The Ansel to be Goodyear welted and there were two key reasons for this. First, Goodyear welting creates a waterproof seal. Most waterproof boots that fail to remain waterproof over time are affixed with glue or cement. These types of barriers break down over time and start to leak. The Ansel uses a leather welt and internal stitching that keeps water out from the day you buy until the day you recycle them. The second reason we wanted to use a Goodyear welt is to allow our boots to be resoleable. High-quality leathers will keep much longer than any rubber sole so we wanted to make sure our product was something you could keep for life.
This is the final product. After over 50 prototypes and dozens of different component combinations, we landed on this strikingly beautiful shoe.
The Ansel is available for purchase via seasonthree.com.
>>> For more footwear options, visit the Design Milk Shop here! <<<