The Rise of 3D-Printed Prefabricated Homes
As construction materials costs increase, builders and developers are seeking alternatives to traditional home construction methods to address housing shortages. In response, an expanding construction technology field is the 3D printing sector. This technology promises quicker, cheaper construction and the potential to extrude local and recycled materials. However, due to the slow-changing nature of the construction industry, a radical shift involving large-scale 3D-printing machines on-site and a complete overhaul of the construction process seems unlikely shortly.
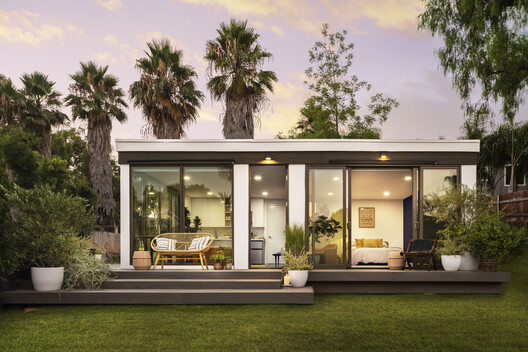
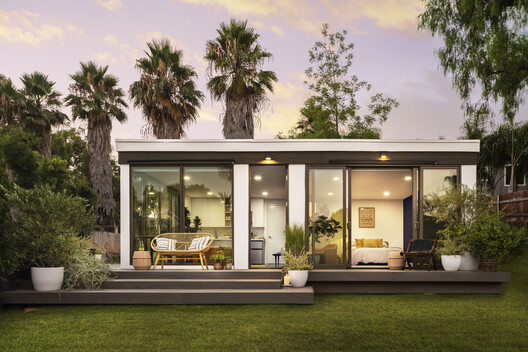
As construction materials costs increase, builders and developers are seeking alternatives to traditional home construction methods to address housing shortages. In response, an expanding construction technology field is the 3D printing sector. This technology promises quicker, cheaper construction and the potential to extrude local and recycled materials. However, due to the slow-changing nature of the construction industry, a radical shift involving large-scale 3D-printing machines on-site and a complete overhaul of the construction process seems unlikely shortly.
Prefabricated 3D printing modular housing offers a compelling solution, providing the benefits of 3D printing advancements while leveraging standard construction machinery and labor. In off-site 3D-printed construction, there is no need to transport massive 3D-printing machines on-site. Instead, components are printed in a controlled environment and then assembled on-site. These types of 3D-printed residential modular kits of parts are already being manufactured and are attracting significant investment.