Screen Printing Vs Laser Printing | Comparison
A laser beam doesn’t damage the printed item and works like a knife to remove the surface material without stress. On the other hand, screen printing is more versatile and suitable for printing on various fabrics or even spherical surfaces. To use the best screen printing machine for your business, you must determine the printing […]
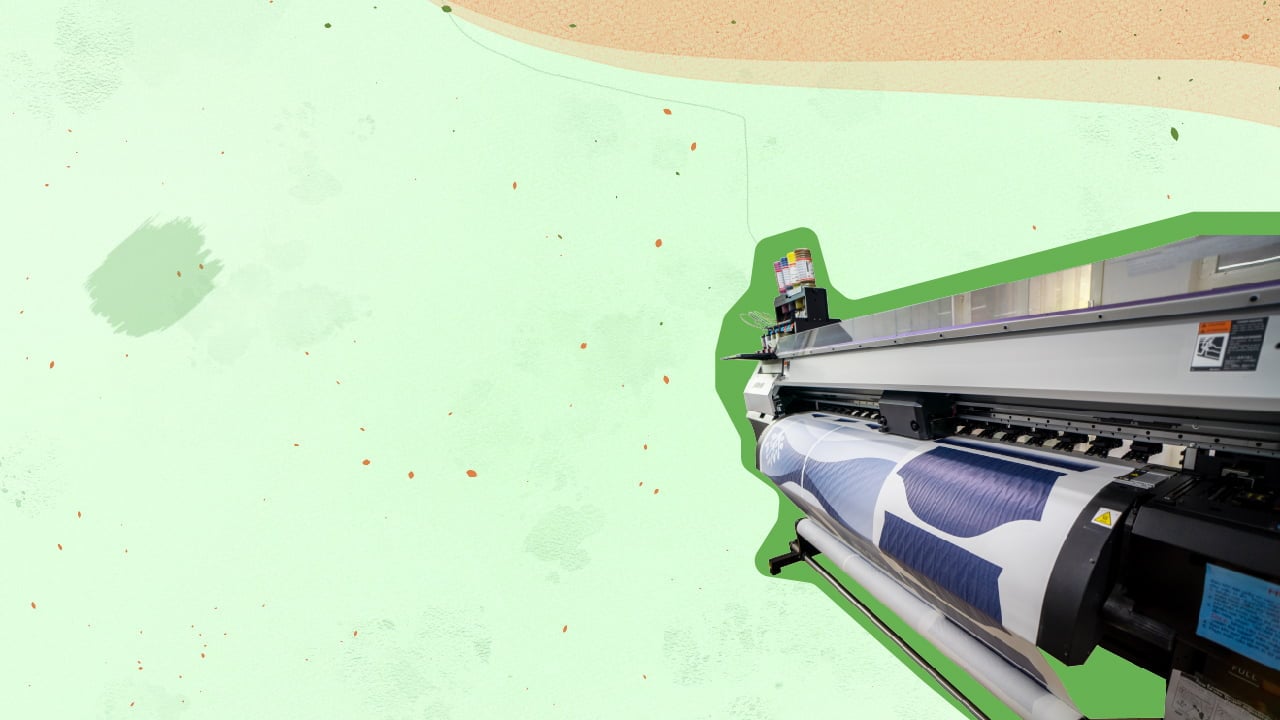
A laser beam doesn’t damage the printed item and works like a knife to remove the surface material without stress. On the other hand, screen printing is more versatile and suitable for printing on various fabrics or even spherical surfaces.
To use the best screen printing machine for your business, you must determine the printing technique first. The two most popular options are screen printing and laser marking, which have several advantages based on the complexity of the printing job.
In today’s guide, I delve into the intricacies of both these methods and determine which technique is better.
What Is Screen Printing?
I have often wondered what is a screen printing machine used for, so I decided to do some digging.
Screen printing is a technique dating back thousands of years, whereby the design is printed on a screen by pushing the screen printing specialty inks through small holes. Also known as silk screen printing, it is a traditional screen printing process most suitable for single-color designs.
You can also use it for multicolor patterns to decorate the surface material, but the printing process takes place in several layers in such instances. But given its overall ease of use, the screen printing business has a large customer base in the apparel industry and comes in handy for printing on textiles by heating the ink.
But it’s not enough to know about the process, so I have listed the main screen printing equipment here –
- Ink
- Squeegee
- Mesh
- Marked surface material
- Stencil
How Does Screen Printing Work?
Screen printing is easy to understand and involves soaking the mesh in ink while the squeegee is attached to the back of the mesh. As the ink flows over the mesh, the squeegee starts moving and presses the mesh against the surface material. This forces the ink through tiny perforations onto a stencil fixed in front of the mesh.
As the silk screening continues and the ink covers the surface, you will find that it replicates the stencil design. But why is it called silk screening? This is because the mesh used to create smooth gradients was once made from silk, but with time polyester has emerged as a better alternative.
I have also seen many screen printing machines use stainless steel and nylon meshes based on the type of application.
What Is Laser Marking?
Laser marking is a digital printing technique known as direct-to-garment printing that uses 4-6 colors to create detailed designs and multicolored patterns. The colors most commonly used for digital printing with a laser beam include –
- Cyan
- Red
- Black
- Yellow
- Magenta
- Green
Best of all, DTG printing doesn’t require complicated equipment and uses a black inkjet printer found in most commercial spaces. And just like screen print, DTG machines print multiple colors on promotional items like customized t-shirts or other garment styles.
But compared to screen printed items, DGT prints are more modern, having been developed some 20 years back. That said, while looking at screen printing machine types, I have realized that even DTG printing is pretty popular, with several high-quality laser printers having been manufactured recently.
Laser marking has become widely accepted, and some initial flaws have been ironed out. However, while screen printing is suitable for various purposes, laser marking is only used by the top companies, given the higher price of the technique.
So, why do organizations use it, then? This is because DTG printers don’t have the effort or setup cost of screen printing. All you need is to overcome the initial manufacturing cost and produce products in limited numbers for the first few months to break even until business booms.
Once you weather the storm, you can even supply on-demand orders with laser printers.
Key Differences In Screen Printing Vs Laser Printing
Before I discuss the advantages of screen printing and laser marking, here’s a summary of what makes each technique popular.
For screen printing, I found that –
- It’s suitable for high-volume orders
- It uses special screen printing inks
- It’s best for single-color prints, such as logos or texts
- Colors are more eye-catching on dark garments
- Screen printing on a large surface area
- Matches the exact colors of the design
- Ideal for printing on synthetic fabrics and polyester
On the other hand, digital printing is better suited for –
- Simple and smaller orders
- Colors are more visible on 100% cotton fabrics
- The print is soft and lightweight
- Subtle elements and intricate skin tones
- Many sizes and print locations
- Smooth photographic elements and color gradients
- Detailed designs
- Multiple blends and colors
Let’s explore these points in further detail below…
1. Color Blending
For those who don’t know, color blending refers to the smoothness of the gradients and the ability to create more colors by mixing only a handful of shades. And this is where DTG prints stand out since the color dots are invisible to the naked eye, provided you use diffusion dither and print at 1200 dpi.
Moreover, a laser printer uses water-based ink, which is semi-transparent compared to plastisol, ensuring that the colors combine easily to create beautiful and smooth gradients. That’s why you can put the subtleties in design with DTG, like smoke fading into a shirt.
But screen printing uses plastisol inks and blends the colors through a technique known as a simulated process. However, color blending accuracy with this method is not as good as DTG, especially when printing tiny elements.
2. Vibrancy
While plastisol affects color blending, it comes in handy for traditional screen printing techniques, thanks to the presence of PVC particles within a plasticizing emulsion. Due to the opaque nature of this spraying ink, it creates a bright, white base for greater vibrancy, especially on dark clothing.
Plus, plastisol inks are available in multiple vibrant shades, which isn’t the case with the water-based inks involved in laser marking. I have noticed a decent base with such inks, but the final result isn’t as great, which gives screen printing the edge.
3. Details
If you want to create a detailed design, DTG printing is much better than screen printing. This is because a well-done DTG print consistently showcases fine lines, subtle elements, and fine textures throughout the surface.
On the other hand, screen printing doesn’t manage to hold the small details as well, and you will need to make some changes.
4. Color Matching
Matching colors is important when manufacturing orders for brands, for which screen printing is the clear favorite as it uses Pantones to duplicate most colors, including super-saturated colors. Moreover, since many brands have guidelines for using Pantones, DTG prints can seem completely out of place.
Screen printing matches the exact colors with ease, while laser marking uses process inks or gamuts which doesn’t guarantee that the most vibrant shades will match. Also, the opaque base means that the color on the shirt might leak through slightly, particularly on darker fabric.
5. Comfort
In terms of comfort, laser marking has a slight edge, given its ability to create soft and lightweight prints. This is especially important when designing dark shirts because the detailing and shades on such color garments are usually more.
Using too much color often affects the breathability and flexibility of the fabric, leading to sweat patches that laser marking helps avoid. You can also achieve similar results with screen printing by using a soft hand so that the ink comes out smoother for the shirt to be lightweight.
Another screen printing technique you can use is the distress effect which reduces the amount of ink covering the surface. But it doesn’t look right on all designs, so DTG is the better choice and is easier to use when comfort is your priority.
6. Durability
Durability is the ability of the print to retain its quality for a long time, something that laser marking cannot guarantee. In most cases, the color fades quickly from DTG printing, but that’s not the case with screen printing, provided you do it right.
The trick is to ensure that the ink is applied properly and heat pressed for curing to guarantee the plastisol doesn’t fade fast. So, if you have a t-shirt that has retained its color and design for several years, it’s probably been screen printed.
7. Consistency
When you receive an order for several t-shirts that need to look the same, trust DTG printing with your eyes closed. It’s possibly the best printing technique to generate multiple identical designs because the printer reads the digital file and replicates it directly onto the shirt.
In contrast, achieving the same consistency with screen printing is challenging since there are several factors at play, including –
- Mesh type
- Screen tension
- Dot gain
- Ink viscosity
- Squeegee sharpness
- Flash dry temperature
- Registration
- Pressure and angle
So, ensuring that all these factors are exactly right for every print is almost impossible, and that’s why there are more variations.
8. Versatility
The versatility of a printing process depends on the textile type, print locations, garment style, and placements. But screen printing is regarded as the more versatile option because its manual operation offers greater flexibility.
More importantly, DTG doesn’t work on all fabrics, locations, or product types, while screen printing works with most color garments, and there are fewer restrictions in terms of locations.
Screen Printing Vs Laser Printing Conclusion
Both screen printing and laser marking have their pros and cons, so which technique you use depends on the size of the order, garment type, design, and client’s requirements. As a rule, it would be best to use screen printing for bulk orders, given its greater flexibility and affordability than laser marking.
But when the design is important, and you need to bring out the small details on several products, laser marking is the better choice. My suggestion would be to at least use the best quality inks and let the design cure properly to achieve the desired results.
Tip
Many printing companies suggest you increase the text or image size to hide flaws in the small details when screen printing. And despite both techniques using halftones for the best results, setting laser marking prints at 1200 dpi makes the design elements more prominent.